Materiales de construcción hechos con cáscara de huevo y otros residuos
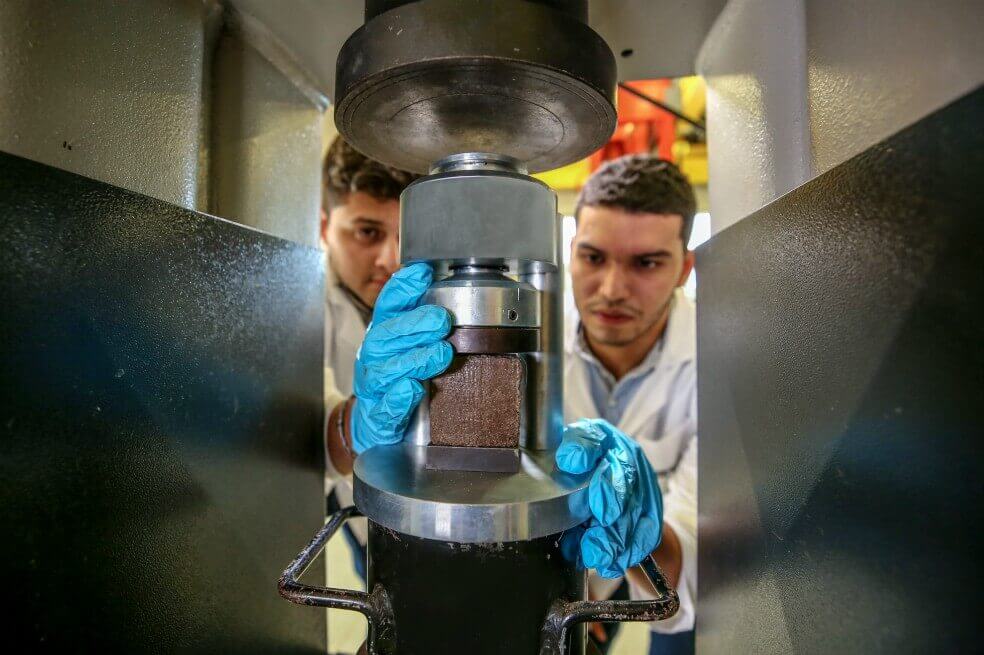
Aplicar la economía circular a los desechos de la industria y del consumo humano ha abierto alternativas para hacer más sostenible uno de los sectores claves de las sociedades modernas, pero de los más contaminantes: la construcción.
“El puente está quebrado, ¿con qué lo curaremos? Con cáscaras de huevo…”. ¿Cáscaras de huevo? Así mismo: Carlos Pacheco, docente e investigador del Instituto para el Desarrollo Sostenible (IDS) de la Universidad del Norte, se tomó en serio la ronda infantil, y encontró la forma de incorporar las cáscaras de huevo que normalmente van a parar a la basura, al cemento usado en la construcción.
Pero no solo las cáscaras de huevo, también los residuos de PVC industrial y la tóxica granalla. Carlos y sus estudiantes se propusieron reemplazar elementos con los que se fabrican cada material imprescindible para la construcción. Cáscara de huevo para el cemento. PVC para el mortero. Granalla para el mortero y el concreto. Un ejemplo clásico de economía circular.
Todo porque construir contamina. “El sector de la infraestructura es uno de los mayores responsables de las emisiones de CO2 en el mundo”, dice Pacheco. “Por eso queremos contribuir a arreglar este problema”. Solo la industria del cemento produce más del 5 % de este gas a nivel mundial, según el World Business Council for Sustainable Development. Únicamente dos procesos superan estas cifras: la obtención de combustibles fósiles y la explotación de la tierra.
Ya no hay margen de espera, el planeta urge de soluciones que mitiguen la afectación al medioambiente, pero es poco probable que en las ciudades se deje de construir, pues este sector es un dinamizador de las economías; de hecho, de acuerdo con un informe del Fondo Monetario Internacional, en 2018 será crucial para el crecimiento del PIB de Colombia. La pregunta entonces es: ¿cómo construir más y contaminar menos? Carlos Pacheco planteó ese problema en una sus clases de ingeniería y con ayuda del profesor Andrés Guzmán y un grupo de estudiantes la idea empieza a cuajar en opciones reales.
Y es más simple de lo que parece: reemplazar con materiales de desecho agroindustrial la mezcla con la cual se hace cemento u otros materiales derivados del mismo. Países como Alemania han avanzado en investigaciones al respecto, pero en Colombia solo cinco universidades trabajan actualmente el tema. En el Caribe, Uninorte es la única. De acuerdo con Pacheco, no todo el cemento se usa para lo mismo. El cemento básico, el polvo gris que casi todo el mundo conoce, se obtiene de tres elementos: óxido de calcio, silicio y aluminio. A partir de este cemento básico se producen dos materiales indispensables en la construcción: el concreto y el mortero.
El concreto, que usualmente se utiliza como la base sólida de casi cualquier construcción es una mezcla entre cemento, agua, agregado fino (arena) y agregado grueso (piedras o gravilla). El mortero, que es exactamente la misma combinación, pero sin el agregado grueso, se usa como mezcla para pegar bloques y ladrillos o hacer adoquines para aceras. Con ayuda de investigadores del IDS, estudiantes e, inclusive, egresados, el proyecto inicial de Pacheco fue remplazar el cemento con cáscaras de huevo.
Cáscara de huevo
Esa fue la primera investigación de donde surgió todo el proyecto de reemplazo de materiales. En 2015, en una clase de ingeniería civil de Pacheco, los estudiantes Estiven Frías, Francisco Gómez y Viandy Bravo propusieron un proyecto basado en economía circular para reutilizar recursos que en la actualidad son desechados.
Los jóvenes buscaban reemplazar elementos básicos que hacen parte de la mezcla de cemento y lo lograron. Luego de pasar por un proceso de incineración de las cáscaras de huevo para eliminar todos los residuos orgánicos, consiguieron reemplazar con éxito un 5 % del calcio utilizado para hacer cemento sin afectar las propiedades de la mezcla. Y aunque parezca poco, en un escenario macroindustrial el impacto es enorme.
Tan solo el año pasado se consumieron en el país 13 827 millones de huevos, una cifra que coloca a Colombia como el tercer mayor consumidor de este producto en Latinoamérica, solo superado por México y Brasil, según la Federación Nacional de Avicultores (Fenavi). Todas esas cáscaras van a parar a desechos sanitarios cuando su vida útil puede que no haya terminado allí.
Además, la extracción de calcio de la tierra implica su explotación en grandes canteras, un proceso más contaminante que la construcción misma, y que no solo causa graves afectaciones en el ambiente, sino que parte de la extracción de un recurso no renovable, que con los años se ha ido acabando por la extracción indiscriminada. “Destruimos toda una montaña para hacer un edificio y eso genera muchos impactos ambientales como deforestación, cambio de aguas superficiales, contaminación de ríos, exposición de material particulado a la población civil”, explica Pacheco.
La investigación, que aún no culmina, obtuvo un reconocimiento meritorio en el XX Encuentro Nacional y XIV Internacional de Semilleros de Investigación, realizado del 12 al 15 de octubre de 2017 en Barranquilla, y ganó como mejor ponencia en la Conferencia Internacional de Ingeniería Ingenio 2018. El trabajo que sigue es igual de complejo: conseguir reemplazar con otros residuos agroindustriales los demás elementos con los que se hace cemento.
En eso están concentrados los investigadores, que, aunque próximos a graduarse, pretenden seguir con el proyecto con apoyo del IDS. Las pruebas buscan ahora conseguir en total un reemplazo del 15 % de la mezcla del cemento. Gómez señala que, tras encontrar calcio en la cáscara de huevo, ahora se enfocarán en un residuo que pueda proveer silicio, encargado de entregar la resistencia al concreto. Entre ellos probarán cáscara de piña, cáscara de banano y cascarilla de arroz como sus primeros pilotos.
El PVC industrial, un material que no se degrada
La producción de residuos de PVC industrial fue la que terminó concretando esta investigación. La problemática, que fue planteada a Pacheco por la empresa Tecnipozos, era que al realizar cortes en la tubería de alta densidad para agua potable que se iba a instalar en Barranquilla, se generarían residuos en forma de fibras que por su composición no se degradan.
El docente llevó el problema al aula de clase y allí, con estudiantes que en la actualidad han realizado maestrías con enfoques en ingeniería ambiental, encontraron la solución. Luego de distintos ensayos lograron reemplazar 30 % de la mezcla para hacer mortero, cambiando el agregado fino (arena) por este residuo.
Sin embargo, en este caso, las sobras de PVC no funcionaron para incorporarse al concreto debido a que bajaba demasiado la resistencia, afectando la idoneidad de la mezcla. Pacheco explica que aun así el impacto es enorme, porque se reutiliza un desecho que parecía no tener algún uso posible y que en cambio puede, por ejemplo, implementarse para la producción de adoquines para personas invidentes.
“Con ese proyecto hicimos varias cosas positivas: le dimos una parte de durabilidad al mismo elemento, porque no se degrada nunca y no estamos botando esto a un relleno sanitario. Le solucionamos el problema a una empresa, reduciendo el impacto ambiental. Lo que nos falta es seguir el proceso de masificación y revisar el tema de abrasión y desgaste; para eso estamos buscando estudiantes que quieran sumarse a la fase final de la investigación”, destacó el docente.
Granalla, un residuo peligroso
La granalla es un residuo complejo debido a su alto contenido contaminante, que resulta incluso nocivo para la salud.
El material, que es en sí un abrasivo en forma de pequeñas virutas metálicas utilizadas para limpiar piezas de fundición y para cortar bloques de granito, contiene luego de su uso residuos de pintura, grasa y aceites que lo hacen altamente contaminante. Sin embargo, luego de un proceso de lavado, los investigadores encontraron que no solo se podía utilizar, sino que tenía un alto contenido de reemplazo tanto en mortero como en concreto.
La idea de reutilizarlo nació de la tesis de maestría en Ingeniería Ambiental de Hernando Cabrera, un estudiante que estuvo en el proyecto de PVC industrial y que posteriormente al terminar su pregrado decidió enfocar su formación en esta área.
Explica Pacheco que generalmente lo que se hace con la granalla es encapsularla dentro de tanques con cemento y disponerla en celdas de seguridad o minas de sal, donde permanecerá para siempre. “Nosotros comenzamos con el proceso de reemplazamiento de materiales y encontramos que tenía hasta un 30 % de reemplazo con muy buena resistencia”.
Con ese resultado surgieron dos grandes preocupaciones. La primera era el peso que sumaba a la mezcla este elemento metálico. Lo resolvieron delimitando su uso solo en elementos pequeños donde se necesite un concreto denso, como anclajes de puentes colgantes. Utilizarlo en la estructura de un edificio no sería viable debido a lo pesadas que resultarían las columnas.
La segunda era saber si al momento de poner la mezcla en el suelo, el cemento podría degradarse y los elementos presentes en la granalla podrían contaminar el suelo. Luego de distintas pruebas en laboratorio donde se probó la lixiviación —el proceso mediante el cual se prueba si un líquido puede atravesar un sólido y diluir sus componentes— se encontró que no tenía problema alguno.
Lo que viene
Encontrar soluciones importantes para lograr un modelo de construcción sostenible es un tema que en la actualidad atañe al gobierno, la academia y organizaciones en pro del medioambiente y la industria misma. En 2017, por ejemplo, se realizó en París el Simposio Internacional “El futuro del cemento”, organizado por la Unesco. Expertos e investigadores de distintos países se reunieron para discutir alternativas al respecto de la producción eficiente y sostenible de hormigón.
Colombia debe empezar a preocuparse. El desarrollo en infraestructura es actualmente uno de los pilares de la economía, pero la contaminación producida por estas nuevas obras puede llevar a que el país incumpla compromisos como la reducción en un 20 % de su emisión de gases de efecto invernadero antes del 2030, pactados en el Acuerdo de París Sobre el Cambio Climático.
Pacheco y Guzmán siguen trabajando en distintos proyectos, como mortero hecho con yuca. Por ahora aún falta mucho por investigar en las cáscaras de huevo y el PVC industrial. En cuanto a la granalla solo es necesario la intención de industrializar el proceso para hacer concreto o mortero, reemplazando la mezcla con este residuo. Mientras tanto mundialmente la preocupación por el medioambiente sigue creciendo.